Obróbka skrawaniem
Obróbka skrawaniem jest terminem niezwykle szerokim i z tego względu artykuł ten podzielony został na części, z których każda obejmuje różne jej formy.
Ta część artykułu pojawi się później
Ta część artykułu pojawi się później
Ta część artykułu pojawi się później
Ta część artykułu pojawi się później
W procesie ścierania mamy doczynienia z wieloma ostrzami o bliżej nieokreślonej geometrii, które dokonują procesu skrawania i umieszczone są na ściernicy. Ściernica zbudowana jest z dwóch zasadniczych elementów:
- ścierniwa - materiał ścierny o właściwościach ostrzy skrawających posiadający określone wymiary i kształt,
- spoiwa – materiał wiążący cząsteczki ścierniwa.
Ścierniwo może być zbudowane z różnego rodzaju materiałów, wśród których wymienić możemy m.in.:
- Elektrokorund czyli Al2O3 posiada twardość 9 w skali Mohsa, który w zależności od poziomu zanieczyszczeń i dodatków podzielić można na:
- Zwykły (brązowy) oznaczany jako 95A zawiera 95% Al2O3 i jest najbardziej wytrzymały spośród elektrokorundów. Stosowany jest do zgrubnego szlifowania niskostopowych stali, stali nierdzewnych, żeliwa.
- Półszlachetny (szary) oznaczany jako 97A zawiera 97% tlenku glinu charakteryzuje się średnią twardością i wytrzymałością. Stosowany jest do szlifowania precyzyjnego i narzędzi.
- Szlachetny (biały) oznaczany jako 99A zawiera 99% Al2O3 charakteryzuje się dużą twardością i kruchością. Stosowany jest do szlifowania precyzyjnego w śród, którego wymienić możemy m.in. szlifowanie płaszczyzn, cylindryczne, narzędzi skrawających.
- Chromowy oznaczany jako CrA to połączenie tlenku glinu oraz kilku procent tlenku chromu. Charakteryzuje się dużą twardością i wytrzymałością. Stosowany jest do szlifowania stali wysokostopowych i do ostrzenia narzędzi skrawających.
- Cyrkonowy oznaczany jako ZrA otrzymywany jest poprzez dodanie do Al2O3 tlenku cyrkonu i charakteryzuje się największą wytrzymałością mechaniczną i ciągliwością. Stosowany jest do wysokowydajnego szlifowania żeliwa, półfabrykatów stalowych z dużymi naciskami.
- Węglik krzemu zwany karborundem i oznaczany poprzez SiC otrzymywany z piasku kwarcowego oraz koksu naftowego w piecach oporowych posiada twardość 9,5 w skali Mohsa. Drugi po diamencie pod względem twardości. W zależności od zanieczyszczeń i dodatków dzieli się on na:
- Zielony oznaczany jako 99C zawiera minimum 99% węglika krzemu. Stosowany jest do szlifowania węglików spiekanych, ceramiki.
- Czarny oznaczany jako 98C zawiera 98% SiC stosowany jest do szlifowania węglików spiekanych, betonu, materiałów ceramicznych, kamieni do zgrubnego szlifowania modeli żeliwnych oraz przecinania betonu, kamienia i żeliwa szarego.
- Borazon czyli BN lub CBN stosuje się do szlifowania narzędzi wykonanych z bardzo twardych stopów stali tj. stal chromowa czy narzędziowa oraz przy precyzyjnym cięciu.
- Diament naturalny oznaczany jako D posiada twardość 10 w skali Mohsa. Oddaje najlepiej ciepło spośród wszystkich ścierniw oraz posiada ostre krawędzie i dobrą łupliwość. Dobrze nadaje się do obróbki żelaza o ile temperatura pracy nie przekracza 720°C.
- Diament sztuczny oznaczany jako DS zastępuje naturalny gdyż posiada takie same jak on właściwości.
Spoiwa podzielić zaś można na:
- ceramiczne (V),
- żywiczne (E dla naturalnych i B dla sztucznych),
- gumowe (R),
- metalowe (M),
- klejowe (KS),
- krzemianowe (K),
- magnezytowe (MG).
Znając podstawy budowy ściernic dobrze jest zapoznać się z sposobem ich oznaczeń, które dzieli się na trzy grupy oddzielone myślnikami, które opisują kolejno:
- typ, zarys (kształt ściernicy) oraz wymiar,
- charakterystykę techniczną,
- dopuszczalną prędkość roboczą.
Dokładniejszy opis oznaczeń ściernic przedstawiony został na poniższym schemacie 1.
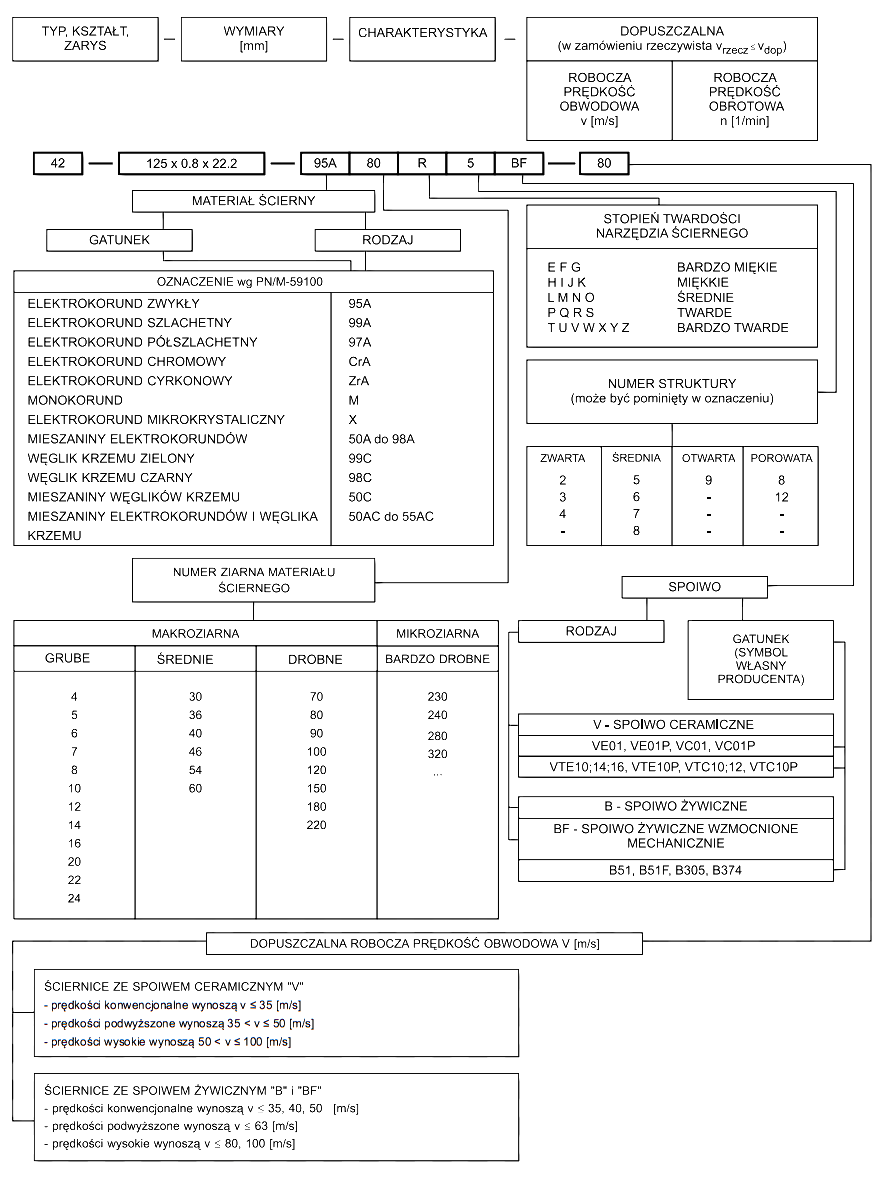
Schemat 1 przedstawia sposób oznaczenia ścernic.
Jak widzimy jest on bardzo rozbudowany i pozwala przez to na dobranie ściernicy do potrzeb.
W wyniku procesu szlifowania dochodzi do zużycia ściernicy, które to ma cztery zasadnicze przyczyny przedstawione na rysunku 1.

Rysunek 1 przedstawia sposoby zużywania ściernicy.
Przyczyną tępienia się ziaren są siły tarcia, adhezja, dyfuzja oraz procesy chemiczne, które to zachodzą w wysokiej temperaturze. Tępienie się ostrza powoduje wzrost oporów skrawania oraz temperatury.
Po przekroczeniu doraźnej wytrzymałości ziaren dochodzi do ich pękania co powoduje odsłonięcie nowych ostrych krawędzi ścierniwa co obniża opory skrawania i poprawia parametry obrobionej powierzchni. Im materiał daje drobniejsze wykruszenia tym odsłania więcej krawędzi skrawających a przez to długość pracy i ilość usuniętego materiału przez ziarno jest większa. Proces ten pozwala również na ostrzenie ściernicy.
Gdy dochodzi do przekroczenia wytrzymałości spoiwa, ziarna zostają wyrwane z ściernicy. Wpływ na ten proces ma również erozja spowodowana nacierającymi wiórami, które, jeśli poddawane są dużym naciskom oraz temperaturze zgrzewają się nie pozwalając na wyrywanie ziaren a pogarszają parametry powierzchni skrawanej. Jeśli spoiwo jest zbyt miękkie to dochodzi wtedy do zbyt szybkiego wyrwania ziaren a w konsekwencji spadku średnicy całej ściernicy, gdy mamy do czynienia z sytuacją odwrotną tj. zbyt twardym spoiwem ziarna nie są wyrywane w porę co powoduje powstawanie większych oporów skrawania i konieczności częstego ostrzenia ściernicy.
Podczas obwodowej pracy ściernicy najmocniej zużywają się krawędzie co powoduje zmniejszenie powierzchni roboczej ściernicy dodatkowo ze względu na nierówną jej twardość dochodzi do powstawania błędu okrągłości ściernicy. Aby zlikwidować błąd okrągłości, oczyścić pory i naostrzyć ścierniwo dokonuje się procesu zwanego obciąganiem.
Szybkość zużycia zależy od tego czy ściernica wykorzystywana jest do obróbki wstępnej (z dużymi głębokościami) czy wykończeniowej. Przy tej pierwszej ziarna ścierniwa wypadają, kiedy jeszcze nie są mocno stępione a drugiej dopiero po znacznym stępieniu z czego można wyciągnąć wniosek, że w przypadku pierwszej obróbki ściernica zużywa się znacznie szybciej. Znaczenie ma również obecność cieczy obróbkowej, która podawana pod wysokim ciśnieniem oczyszcza pory z wióra dając dłuższy okres trwałości ściernicy (czyli interwał między kolejnymi obciągnięciami).
Jednym z sposobów obciągania ściernicy jest ta wykorzystująca diamentowy obciągacz jednoziarnisty. Proces ten przedstawiony został na rysunku 2.
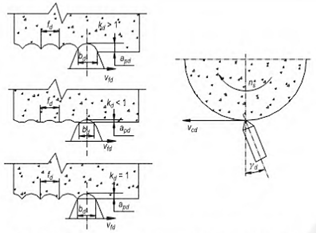
Rysunek 2 przedstawia proces obciągania ściernicy diamentowym obciągaczem jednoziarnistym.
Na końcu obciągacza zamontowane jest ziarno diamentu pochylone względem promienia ściernicy pod kątem γd mającym wartość w zakresie od 10 do 15°. Kryształ ten wykonuje ruch równoległy do osi i styczny do powierzchni ściernicy vfd zagłębiając się przy tym na głębokość apd. Wymiar opisany na rysunku jako bd to czynna szerokość ziarna. Diament podczas obróbki powoduje wykruszenia ziaren, wyrwania ich oraz pęknięcia spoiny i ścierniwa. Ze względu na znaczne koszty takiego procesu związane z cenami diamentów o odpowiedniej ilości karatów proces ten wykorzystuje się głównie do obciągania ściernic służących szlifowaniu dokładnych śrub czy kół zębatych.
Zamiast nich częściej wykorzystuje się obciągacze wieloziarniste, które charakteryzują się dwoma rodzajami struktur, gdzie w pierwszej wydłużone ziarna umieszczone są rzędami lub warstwami w spoiwie metalowym a drugiej bardzo drobne ziarna diamentu zalane są spoiwem metalowym.
Do obciągania ściernic o skomplikowanych kształtach w produkcji seryjnej stosuje się obciągacze obrotowe kształtowe, w których obciągacz ma formę rolki o odpowiednim zarysie z nasypem diamentowym i wykonuje ruch obrotowy oraz posuw promieniowy. Przebieg tej czynności zaprezentowany został na rysunku 3.
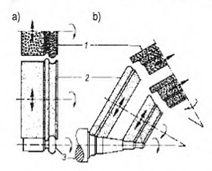
Rysunek 3 przedstawia proces obciągania obciągaczem obrotowym kształtowym. Podpunkt a) prezentuje obciąganie pojedynczej ściernicy zaś b) zespołu dwóch ściernic. Jako 1 zilustrowano obciągacze, 2 ściernice a 3 wałek obrabiany.
W produkcji małoseryjnej wykorzystuje się obciągacze rotacyjne punktowe, które napędza się poprzez tarcie. Ostrzenie się takiej ściernicy jest w tym wypadku wynikiem powstania nacisków powierzchniowych powstających pod wpływem punktowego nacisku obciągacza. Proces ten przedstawiony został na rysunku 4.
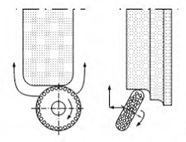
Rysunek 4 przedstawia proces obciągania przy pomocy rotacyjnego obciągacza punktowego.
Źródła
- Andre abrasive articles, katalog narzędzi ściernych (dostęp: 9.05.2023r.)
- EBMIA, Ściernice do ostrzenia pił SZLIFF BORAZON (dostęp: 9.05.2023r.)
- K. Mogielnicki, Instrukcja do zajęć laboratoryjnych z przedmiotu: techniki wytwarzania ćwiczenie nr: 8 szlifowanie płaszczyzn, 2016, Białystok
- P. Cichosz - Narzędzia skrawające, 2006, Warszawa
- W. Olszak, Obróbka Skrawaniem, 2009, Warszawa