Spajalnictwo
Spajaclnictwo jest pojęciem bardzo rozległym jednak wszystkich jego przedstawicieli łączy (poza nielicznymi wyjątkami) proces nagrzewania łączonych elementów. Ze względu na różnice w źródle ciepła, spoiwo lub jego brak możemy podzielić je na:
Za najstarsze spawalnicze źródło ciepła uznaje się płomień jednak to dopiero patent z 1862 r. na spawanie łukiem elektrycznym przy pomocy elektrody oraz udana próba skroplenia tlenu w 1883 r. przez Polaków – Zygmunta Wróblewskiego i Karola Olszewskiego rozpoczęła masowe stosowanie spawalnictwa.
W procesie spawania można zastosować kilka źródeł ciepła i wymienia się wśród nich:
- płomień gazowy,
- łuk elektryczny,
- wiązkę promieniowania elektromagnetycznego,
- bombardowanie elektronami lub innymi cząstkami o wysokiej energii.
Główną metodą w spawaniu gazowym jest spawanie palnikiem acetylenowo tlenowym a inne tj. spawanie palnikiem acetylenowo-powietrznym, propanowo-tlenowym, wodorowo-tlenowym czy metyloacetylenowo-tlenowym stosowane są rzadko gdyż wadą ich jest brak możliwości regulacji charakteru płomienia (utleniający, redukujący i neutralny) oraz niska temperatura płomienia. Z tego względu w dalszej części omawiania metody spawania wykorzystującej płomień gazowy skupimy się na spawaniu acetylenowo-tlenowym.
Spawanie palnikiem acetylenowo-tlenowym pozwala na regulację charakteru płomienia, posiada najwyższą temperaturę płomienia, prędkość spalania oraz korzystny rozkład ciepła w płomieniu. Stosowane może być w warunkach warsztatowych i polowych a palnik oprócz spawania może być wykorzystywany także przy cięciu tlenowym, podgrzewaniu i lutowaniu. Z reguły spawa się nim blachy od około 0,4mm do 10mm wykonane z stali, żeliw, aluminium, miedzi, niklu i ich stopów. Do istotnych wad spawania palnikiem acetylenowo-tlenowym należą niska jakość uzyskiwanego połączenia (pod względem metalurgicznym i mechanicznym), mała wydajność, silnie utleniona i przegrzana strefa wpływu ciepła i duże odkształcenia cieplne spawanych elementów. Nie spotyka się go teraz w przemyśle a jedynie pracach instalacyjnych i remontowych.
Metoda łuku elektrycznego jest wyładowaniem elektrycznym w atmosferze zjonizowanych par i gazów, które mogą pochodzić z żużli i topników, gazów ochronnych lub powietrza. Jego częste stosowanie wynika z skoncentrowania ciepła przez niego wydzielanego oraz temperatury, która w wypadku spawania plazmowego dochodzi do 30 000°C. Zakres natężeń jaki spotyka się w spawarkach elektrycznych wacha się od ułamków ampera do nawet kilku tysięcy amperów a napięcia wynoszą od kilku do 50 woltów. Łuk elektryczny oprócz tego, że topi materiał rodzimy i spoiwo (będące samą elektrodą lub podawane jest w formie drutu) usuwa również trudnotopliwe tlenki. Najważniejszymi parametrami podczas spawania łukowego są napięcie, gęstość, natężenie prądu oraz długość łuku.
Jedną z metod spawania łukiem elektrycznym jest spawanie elektrodą otuloną. W metodzie tej stosuje się zasadę, że natężenie prądu powinno wynosić od 30 do 40 razy więcej niż średnica elektrody wyrażona w milimetrach. Podanie zbyt niskiego natężenia powoduje niestabilne jarzenie się łuku a zbyt wysokie odpryski i przegrzanie otuliny. Przy spawaniu prądem stałym istotne jest prawidłowe podłączenie biegunów zasilania, gdyż 65% całkowitego ciepła wydziela się na biegunie dodatnim co ma wpływ na prędkość stapiania elektrody i głębokość wtopienia w materiał spawany. Temperatura na biegunie dodatnim wynosi od 3000°C do 4000°C a ujemnym od 2500°C do 3000°C. W wypadku spawania prądem przemiennym ciepło rozkłada się równomiernie, ale łuk jest mniej stabilny. Maksymalna temperatura w łuku elektrycznym w tej metodzie wynosi 5000°C.
W łuku elektrycznym dochodzi do ciągłych procesów jonizacji i powstawania głównie dodatnio naładowanych cząstek oraz ich neutralizacji. Wraz z wzrostem temperatury oraz natężenia pola elektrycznego zwiększa się poziom jonizacji a zatem i przewodnictwa elektrycznego łuku. Najchętniej jonizują się związki potasu i sodu oraz ogólnie potasowców, które zawarte są w otulinie elektrod otulonych a najgorzej hel co wymusza wysokie napięcie przy spawaniu. Przy wyższych stopniach zjonizowania rośnie stabilność łuku oraz przewodnictwo cieplne, które pozwala bardziej efektywnie nagrzać spawane elementy. Najlepiej ciepło przewodzi wodór następnie hel, azot i argon.
Łuk elektryczny podczas spawania zainicjować można na dwa sposoby a mianowicie:
- zbliżając elektrodę do elementu spawanego – sytuacja ta może zajść tylko wówczas, gdy mamy do czynienia z jonizatorem generującym napięcie kilku tysięcy woltów z dużą częstotliwością.
- stykając elektrodę z elementem spawanym i następnie oddalając ją od niego – w wyniku zetknięcia elektrody z materiałem spawanym dochodzi do nagrzania elektrody i materiału co wspomaga jonizację powietrza i emisję elektronów dzięki czemu może dojść do powstania łuku elektrycznego przy napięciu nie dochodzącym do 80V.
Metodę spawania elektrodowego stosuje się do blach od grubości wynoszącej 1,5mm do około 4mm wykonanych głównie z stali niestopowych i stopowych, żeliw, niklu, miedzi i ich stopów (do każdego należy dobrać odpowiednią elektrodę) dla każdego rodzaju złącz. Szybkość spawania jest niska a jakość spoiny mocno zależy od umiejętności spawacza. Przy tym typie spawania należy pamiętać o zakładaniu maski spawalniczej ze względu na dużą ilość generowanego promieniowania elektromagnetycznego w tym nadfioletowego, które to w krótkim czasie powoduje silne bóle oczu a długim może doprowadzić do utraty wzroku.
Nazwa technologii spawania MIG wywodzi się od angielskiego zwrotu Metal Inert Gas co oznacza, że spraw wykonywany jest w osłonie gazów obojętnych Argonu lub Helu albo mieszanki obydwu tych gazów zaś MAG wywodzi się od anielskiego zwrotu Metal Active Gas co oznacza, że spawanie jest wykonywane w osłonie gazów aktywnych w formie dwutlenku węgla, tlenu, wodoru i azotu lub jednego z wymienionych zmieszanego z argonem lub helem. Ciepło niezbędne do stopienia materiału łączonego oraz spoiwa pochodzi z łuku elektrycznego a spoiwo z topienia się elektrody (z reguły jest to anoda) w formie drutu nawiniętego na szpulę. Drut ten może być lity, proszkowy z rdzeniem topnikowym oraz metalowym zazwyczaj jednak używa się drutów litych. Drut ten ma średnicę od 0,8 do 1,6mm i podawany jest automatycznie z zadaną prędkością zależną od oczekiwanej wydajności procesu oraz natężenia prądu. W nowoczesnej odmianie tego procesu oznaczanej jako CMT (Cold Metal Transfer) drut jest cofany w wypadku zwarcia co zwiększa stabilność łuku.
Opis stanowisko do spawania metodą MIG-MAG przedstawiony został na poniższej grafice.
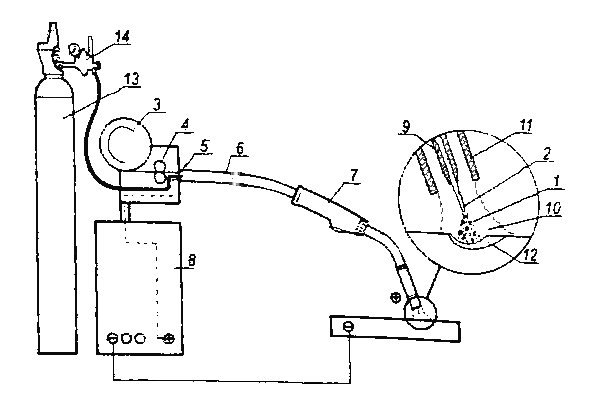
Grafika 1 przedstawia stanowisko do spawania MIG-MAG.
- kropla ciekłego metalu;
- drut elektrodowy;
- szpula z drutem posiada znormalizowane wymiary D-100, D-200, D-300 o masie od 1 do 15kg;
- rolki podające drut podajnika drutu elektrodowego mogą być wbudowane w migomat lub być oddzielnym urządzeniem;
- złącze szafki z przewodem, którym często jest eurogniazdo;
- przewód kompaktowy doprowadza drut, prąd, gaz osłonowy i opcjonalnie ciecz chłodzącą;
- uchwyt spawalniczy;
- źródło prądu z układem sterowania zwane także półautomatem spawalniczym lub migomatem;
- miedziana dysza prądowa;
- gaz osłonowy;
- dysza gazowa;
- jeziorko ciekłego metalu;
- butla z gazem;
- reduktora gazu z przepływomierzem.
W spawaniu MIG-MAG bardzo istotne znaczenie ma sposób przechodzenia metalu do jeziorka spawalniczego, które podzielić możemy na trzy rodzaje:
- zwarciowe,
- mieszane zwane też grubo kroplowym,
- natryskowe.
Na charakter tego procesu ma przede wszystkim wpływ natężenie i napięcie łuku oraz skład gazu osłonowego. Przy spawaniu niskim napięciem i natężeniem łuk elektryczny jest krótki przez to krople utworzone z elektrody są duże i prowadzą do zwarcia. Efektem jest dobre wtopienie, niewielki rozprysk i nierówne lico. Ten sposób spawania wykorzystywany jest do cienkich blach ułożonych w każdej pozycji a także grubszych w pozycji pionowej i pułapowej. Przy średniej wartości napięcia i natężenia uzyskujemy charakter grubo kroplowy przepływu elektrody do jeziorka spawalniczego, gdzie mamy do czynienia z niestabilnym jarzeniem łuku elektrycznego, dużym rozpryskiem metalu i nierównym licem spoiny. Zwiększając dalej wartość napięcia i natężenia uzyskujemy charakter natryskowy, gdzie do jeziorka wpadają drobne kropelki jedna za drugą dzięki czemu wzrasta wydajność stapiania drutu, spoina ma głębokie wtopienie, lico jest gładkie a ilość rozprysków wyraźnie mniejsza. Ze względu na dużą objętość jeziorka spawalniczego najlepiej jest tą metodą spawać w pozycji podolnej (leżące blachy itp.). Z tym rodzajem spawania nie mamy do czynienia dla stali, jeśli stężenia gazu w atmosferze ochronnej jest większe niż 20%.
W osłonie argonu, helu lub ich mieszanek można spawać prawie wszystkie metale jednak najczęściej spawa się glin, magnez, miedź, tytan, i cyrkon oraz ich stopy a także stale wysokostopowe, niestopowe i niskostopowe. Stale wysokostopowe najlepiej spawać w argonie lub argonie i helu z dodatkiem 1-3% tlenu lub 2-4% dwutlenku węgla. Stale niestopowe oraz niskostopowe spawa się w atmosferze argonu z dodatkiem 15-25% CO2 lub 10% CO2¬ i 5% O2¬ dzięki czemu wypala się częściowo mangan, krzem i węgiel z stali. W tej metodzie rzadziej niż przy spawaniu elektrodami otulonymi zdarza się pęknięcie na zimno. Jako że hel przewodzi dobrze ciepło zalecany jest do spawania elementów wykonanych z materiałów dobrze przewodzących ciepło lub grubych (zalecany jest dodatek argonu gdyż poprawia on jarzenie się łuku). Podobne właściwości ma wodór, ale on zalecany jest tylko do stali austenitycznych. Na poniższej grafice 2 przedstawiony został kształt wtopienia w zależności od gazu osłonowego.
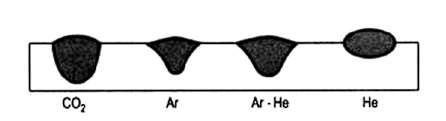
Grafika 2 przedstawia kształt wtopienia w zależności od użytego gazu osłonowego.
Proces MIG-MAG wykorzystuje się także do lutospawania mającego zasady podobne do lutowania twardego, gdzie materiały przygotowuje się jak do spawania jednak sam materiał nie ulega stopieniu podczas procesu. Temperatura procesu wynosi od 850 do 1050°C. Metodę tą wykorzystuje się do łączenia stali ocynkowanej galwanicznej, aluminium, stali wysokostopowych i materiałów różnoimiennych (np. stal i miedź). Do wyrobów ocynkowanych stosuje się drut na bazie miedzi. Gazem osłonowym jest argon z 1-3% dodatkiem dwutlenku węgla lub 1% dodatkiem tlenu.
Proces zgrzewania to proces spajania dwóch materiałów, w którym złącze uzyskuje się dzięki działającemu samemu dociskowi, dociskowi i temperaturze lub dociskowi i innemu zjawisku fizycznemu np. drganiu ultradźwiękowemu. Zazwyczaj jednak mamy do czynienia z procesem, gdzie występuje docisk oraz wysoka temperatura i na tej odmianie zgrzewania się tu skupimy.
Połączenie dwóch materiałów powstaje dzięki powiązaniu cząsteczek dwóch silnie odkształconych plastycznie materiałów dodatkowo nadtapianych a przez to przemieszczających się. Jeśli podczas procesu zgrzewania nie doszło do nadtopienia to w tworzeniu złącza decydującą rolę mają siły Van der Waalsa i/lub dyfuzja.
W zgrzewaniu rezystancyjnym podstawowymi źródłami oporu przepływu prądu są miejsca styku zgrzewanych metali, elektrod z zgrzewanymi metalami oraz sam zgrzewany materiał. Dzięki tym oporom przepływający prąd elektryczny jest w stanie wygenerować ciepło, które uplastycznia lub stapia zgrzewane materiały. Wśród sposobów zgrzewania rezystancyjnego wymienić możemy:
- zgrzewanie doczołowe:
- oporowe,
- iskrowe,
- zgrzewanie rezystancyjne punktowe,
- zgrzewanie rezystancyjne garbowe,
- zgrzewanie rezystancyjne liniowe,
- zgrzewanie rezystancyjne prądem wielkiej częstotliwości.
Zgrzewanie doczołowe polega na łączeniu przynajmniej jednego elementu całą powierzchnią przekroju np. czoła walca z płytą, choć najlepiej, aby przekrój łączonych elementów był taki sam. Łączone elementy mocuje się w miedzianych elektrodach zwanych szczękami, gdzie jedna jest ruchoma celem wywarcia nacisku jednego czoła na drugie lub wyiskrzenia i z tego właśnie powodu rozróżnia się zgrzewanie rezystancyjne doczołowe oporowe i iskrowe.
Zgrzewania rezystancyjne doczołowe oporowe charakteryzuje się tym, że najpierw czoła zgrzewanych elementów są do siebie dociskane a dopiero po chwili przepływa przez nie prąd. Powoduje to spęcznienia materiału i skrócenie o pewną wartość oznaczaną jako ΔS. Prąd odłącza się pod koniec procesu zgrzewania, gdy osiągnięty zostanie określony naddatek na spęczenie. Naddatek długości łączonych elementów przed procesem zgrzewania wynosić powinien 0,2-0,7 średnicy pręta lub 40-60% materiału wysuniętego z elektrod. Dla elementów o małym przekroju (średnica <=10mm) stosuje się małe naciski 5-20MPa i dużą gęstość prądu 800-800 A/mm2 co skutkuje nadtopieniem w krótkim czasie i wyciśnięcie materiału co z kolei powoduje, że połączenie jest prawie tak samo wytrzymałe jak materiał rodzimy. W przypadku łączenia większych przekrojów (średnica >10mm) stosuje się małe gęstości prądu 200-300 A/mm2 i duże naciski 30-50MPa w wyniku czego nie dochodzi do ich nadtopienia a jedynie znacznego spęcznienia przez co powstaje znaczna ilość tlenków w miejscu łączenia co skutkuje gorszymi właściwościami wytrzymałościowymi. Ten sposób łączenia elementów stosuje się dla drutów i prętów wykonanych z stopowych i niestopowych stali, stopów aluminium i miedzi. Pole przekroju nie powinno przekraczać w wypadku stali 400mm2 a metali dobrze przewodzących ciepło i prąd powinno być jeszcze mniejsze.
Cechą wyróżniającą zgrzewania rezystancyjnego, doczołowego iskrowego jest stapianie czół łączonych elementów i wyrzucenie stopionego metalu w formie iskier skąd wzięła się nazwa tego procesu. Występowanie tego zjawiska wynika z powstawania mostków prądowych między łączonymi elementami na małej powierzchni przez co gęstość prądu jest tak duża, że dochodzi do ich rozerwania a cała powierzchnia czołowa zamienia się w płyny metal. W metodzie tej inaczej niż w wcześniej omawianej najpierw podaje się prąd na elementy łączone a następnie zaczyna się je ku sobie zbliżać. Odmianą zgrzewania rezystancyjnego doczołowego iskrowego jest ta z podgrzewaniem wstępnym, w której przed właściwym procesem wyiskrzenia i łączenia materiałów dochodzi do 5-30 0,5-3s zbliżeń oddzielonych 2-6s przerwą, których celem jest wstępne podgrzanie materiału. Zaletą metody omawianej w tym akapicie jest to, że w odróżnieniu od zgrzewania rezystancyjnego oporowego z przekroju poprzecznym elementów łączonych eliminowane są tlenki oraz nierówności występujące przed procesem zgrzewania dzięki iskrzeniu. Ten rodzaj zgrzewania wykorzystywany jest do łączenia stali konstrukcyjnych, stopowych (także tych wysokostopowych z dodatkiem chromu i niklu), niestopowych, metali nieżelaznych. W przeważającej części łączy się elementy o przekroju nie większym niż 3000mm2 lub gdy mamy do czynienia z cienkościennymi rurami itp. do 6000mm2.
Zgrzewnie rezystancyjne punktowe jest procesem spajania elementów płaskich w postaci najczęściej blach poprzez tworzenie złącza przylgowego zakładkowego lub nakładkowego zgrzeinami w formie oddzielnych punktów. Jest to najczęściej spotykany proces zgrzewania wykorzystywany do łączenia praktycznie wszystkich metali. W zgrzewaniu punktowym w pierwszej kolejności dochodzi do dociśnięcia zgrzewanych materiałów przez elektrody w formie kłów a następnie podania prądu na te elektrody, który powoduje nadtopienie i powstanie jądra zgrzeiny. Następnie prąd jest odłączany a docisk w momencie, gdy materiał ostygnie na tyle, że nie spowoduje to zniszczenia zgrzeiny. Tak przedstawiony proces stosuje się do łączenia stali niskowęglowych niestopowych o grubości poniżej 5mm i cieńszych blach z innych metali. Poza tymi wypadkami procedura różni się w zależności od rodzaju i grubości łączonego metalu. Gęstość prądu dla stali niestopowych wynosi 80-300 A/mm2 dla pola przekroju czoła elektrody a siła nacisku 1-3kN na 1 mm grubości blachy.
W zgrzewaniu rezystancyjnym garbowym na jednym z materiałów łączonych a ściślej na powierzchni styku posiada on wypustki tzw. garby, które dociskane są do drugiego materiału a następnie włączany jest prąd, który uplastycznia lub nawet nadtapia garby, które tworzą jądra zgrzeiny. Garby powinno wykonywać się na tej części, która jest grubsza, twardsza i ma wyższą przewodność cieplną i elektryczną. W zgrzewaniu garbowym należy stosować krótkie czasy podawania prądu i wysokie jego natężenie. Ten sposób zgrzewania stosuje się głównie dla stali konstrukcyjnych dobrze zgrzewalnych choć zdarza się je stosować również dla stali stopowych i innych metali. Proces ten wykorzystywany jest w produkcji wielkoseryjnej ze względu na estetykę łączenia, niskie zużycie energii, wysoką dokładność, wydajność oraz żywotność elektrod.
Ta część artykułu pojawi się później.
Źródła strony
- K. Ferenc – Spawalnictwo, 2007, Warszawa
- J. Pilarczyk - Poradnik inżyniera spawalnictwo tom I, 1983, Warszawa
- Maski spawalnicze – dlaczego są potrzebne i jaką dają ochronę? (portal-budowlany24.pl) (dostęp: 27.07.2023 r.)
- Mija 130 lat od skroplenia tlenu i azotu | Nauka w Polsce (dostęp: 25.05.2023 r.)
- Spawanie MIG/MAG | Dob-Spaw.pl (dostęp: 7.06.2023 r.)
- spawanie_mig_mag.pdf (fachowiec.com) (dostęp: 7.06.2023 r.)
- G. Rogowski – Instrukcja do zajęć laboratoryjnych z przedmiotu techniki wytwarzania spawanie metodą MIG/MAG, 2016, Białystok